​Robotics and Industrial Robots and Asimov's Laws
Introduction -
An industrial robot is a robot that is designed to move materials, parts and tools, and perform a variety of programmed tasks in manufacturing and production settings. Industrial robots are often used to perform tasks that are deemed dangerous or unsuitable for human workers. Industrial robots are very precise in what they are told to do, so they are also used for tasks that require high output and no error. The industrial robot has been in use for about 50 years. Over the years, the industrial robot has developed and has become such a big part of the industrial and manufacturing industry.
What Type of Robot is the Industrial Robot? -
The most common types of industrial robots include articulated robots, SCARA robots and gantry robots. However, the most commonly used term for industrial robots, is robot arms. An articulated robot is a robot which uses rotary joints to access its work space. A SCARA robot or Selective Compliant Assembly Robot Arm, is a robot based on a 4-axis design. A SCARA robot is ideal for high-speed assembly, kitting, packing and other material-handling applications. A Gantry robot is a robot that consists of a manipulator mounted onto an overhead system that allows movement across a horizontal plane. The most commonly term industrial robots are categorized under is a robotic arm. Robotic arm being a mechanical arm that has similar functions to an arm of a human and is usually programmable.
How the The Industrial Robot Works -
There are a number of different types of industrial robots that are being used. A common industrial robot mostly used in the manufacturing industry, is a 6-axis industrial robot. A 6-axis industrial robot has good flexibility, powerful
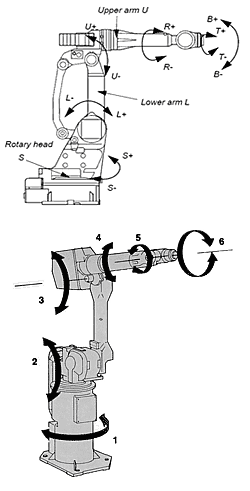
programming software, payload capacities ranging from 5kg up to 1000kg and accuracy to 0.1mm or better. A 6-axis industrial robot consists of two units; the robotic arm and the control system. The robot is called a 6-axis robot simply because the arm has 6-axis, allowing the robot to move any point.
Axis 1 - Axis 1 is located at the base of the robot, and allows it to rotate left and right.
Axis 2 – Axis 2 helps the lower arm of a robot to extend forwards and backwards.
Axis 3 – Axis 3 allows the upper arm of the robot to raise up and lower down.
Axis 4 – Axis 4 rotates the upper arm of the robot in a circular movement.
Axis 5 – Axis 5 allows the wrist of the robots upper arm to raise up and lower down.
Axis 6 – Axis 6 allows the wrist of the upper arm to rotate freely in a circular motion.
The movement is driven by servo motors. Servo motors are self-contained electric devices that rotate or push parts of a machine with great precision. The control system is a computer that allows precise movement of the arm by controlling the power supplied to the motors.
The first programmable industrial robot was designed in 1954 by George Devol. In 1962 the first industrial robot was online and working in a General Motors automobile factory in New Jersey. In 1973 German company KUKA creates the first industrial robot with 6 electromechanically driven axes, electromechanical meaning the device is electronically driven. In 1974 a robotic arm (the silver arm) was created. The robotic arm performed small-parts assembly using feedback from touch pressure sensors. Its creator was Professor Scheinman, informed Vicarm Inc to market a version of the arm for industrial applications. Also in this year industrial robots were developed and installed in Fanuc factory, a robot factory. In 1978 the PUMA (Programmable Universal Machine for Assembly) was created by Vicarm, Unimation. In 1980 the industrial robot industry starts to rapidly grow, with a new robot or company entering the market every month.
The Uses of an Industrial Robot -
Basic operations that industrial robots can undergo are welding, painting, ironing and testing, with all tasks coming with high endurance, speed and precision. However, these applications are only a small part of what industrial robots are capable of. These are the top 5 most common and popular applications for industrial robots.
-
Robotic Handling Operations
-
Robotic machine tending, this refers to the process of feeding parts in and out. Machine tending can be dangerous work that requires a lot of consistency. Making robots do these handling operations, it keeps humans safe from all the injuries that could happen.
-
METAL MACHINING.
-
PLASTIC MOULDING.
-
Robotic Welding
-
SPOT WELDING, which is to join at a number of separate points.
-
ARC WELDING, which is a technique in which metals are welded using the heat generated by an electric arc.
-
Robotic Assembly.
- FIXING, PRESS FITTING, INSERTING, DISASSEMBLING, of robots and vehicles.
-
Robotic Dispensing
-
PAINTING, GLUING, SEALING, SPRAYING.
-
Robotic Processing
-
LAZER, WATER JET CUTTING.
The Future for the Industrial Robot -
What does the future have install for the upcoming industrial robots? These are the upcoming trends that are shaping the future for industrial robots.
-
Cheaper than ever. Industrial robots are flying off the shelves as prices go lower and lower. Standard robot models are now being mass-produced, making them more available for the everyday demand. This accessibility has led a price drop to industrial robots and may. However, can’t get any promises from a 100-dollar robot, so maybe lower prices may be a bad thing?
-
Control made simple. With the new plug and play system, peripherals, robot-models and controllers are made to communicate better with one another. This flexibility makes for an easier industrial robot to control.
-
Increased flexibility. Industrial robots today are able to withstand a number of things or the task they are built or. These things include, the weight the can hold, the distance they can reach etc. However the flexibility of the machines can be increased, so they can hold more, reach further and even be more precise with the work they do.
-
Movement. Most standard industrial robots are placed on a platform that is then remote controlled, in order to move the robot around. Maybe in the future industrial robots will be able to move around the workspace on their own and be able to transport to the place they need to be at, without human help.
Conclusion -
Industrial robots started from just a small idea and are now starting to shape our future. Soon industrial robots will start to take over our workspaces and do all our work for us. Whether this is a good thing or bad thing, no one knows, but it will make life as a human easier and a lot more relaxed. Somewhere in the future maybe there will be a very high unemployment rate because the robots we created are doing our work.
History of the Industrial Robot -
In 1981 a man named Takeo Kanade builds the direct drive arm. The direct drive arm is the first robot arm to have motors installed directly into the joints of the arm. Making it much faster and more accurate than previous robot arms. In 1988 the motoman ERC control system for industrial robots was introduced, with the ability to control up to 12 axes, more than any other controller at the time. In 1996 Nachi (robotics company) expands robotics business, making robotics more known to the world. In 1998 the introduction of the XRC controller allowed the control of up to 27 axes and the synchronized control of three to four robots. The Motoman UP series introduced a simpler robot arm that was more readily accessible for maintenance and repair. Honda was instrumental in driving the development of both the UP series of arms and the XRC arm control.